In the mind of a Fire Protection Design Engineer

Throughout the cause of system design, specifically Wet System design such as Hosereel System, Fire Sprinkler System, Wet Riser System or Standpipe, Hydrant System, Deluge Water Spray, etc., there are many different things are always lingering in the mind of a Fire Protection Design Engineer. Some of which are too important to miss and are essential to produce an effective and workable system and at the same time comply with the requirement of the Local Fire Department and Insurance Companies.
One of the major thought is Pipe Friction lost calculation.
Viscous shear stresses resist the flow of fluid through a pipe within the fluid and the turbulence that occurs along the internal pipe wall, dependent on the roughness of the pipe material.
This resistance is termed pipe friction and is usually measured in feet or metres head of the fluid, which is also referred to as the head loss due to pipe friction.
Head Loss in a Pipe
A large amount of research has been carried out over many years to establish various formulae to calculate the head loss in a pipe. Most of this work has been developed based on experimental data.
Overall head loss in a pipe is affected by several factors, which include the viscosity of the fluid, the size of the internal pipe diameter, the internal roughness of the inner surface of the pipe, the change in elevation between the ends of the pipe and the length of the pipe along which the fluid travels.
Valves and fittings on a pipe also contribute to the overall head loss that occurs. However, these must be calculated separately to the pipe wall friction loss, using modelling pipe fitting losses with k factors.
Darcy Weisbach Formula
The Darcy formula or the Darcy-Weisbach equation as it tends to be referred to is now accepted as the most accurate pipe friction loss formula. Although more difficult to calculate and use than other friction loss formula, with the introduction of computers, it has become the standard equation for hydraulic engineers.
Weisbach first proposed the relationship that we now know as the Darcy-Weisbach equation or the Darcy-Weisbach formula for calculating friction loss in a pipe.
Darcy-Weisbach equation: hf = f (L/D) x (v^2/2g) where: hf = head loss (m) f = friction factor L = length of pipe work (m) d = inner diameter of pipe work (m) v = velocity of fluid (m/s) g = acceleration due to gravity (m/s²) or: hf = head loss (ft) f = friction factor L = length of pipe work (ft) d = inner diameter of pipe work (ft) v = velocity of fluid (ft/s) g = acceleration due to gravity (ft/s²)
However, the establishment of the friction factors was still unresolved. It indeed was an issue that needed further work to develop a solution, such as that produced by the Colebrook-White formula and the data presented in the Moody chart.
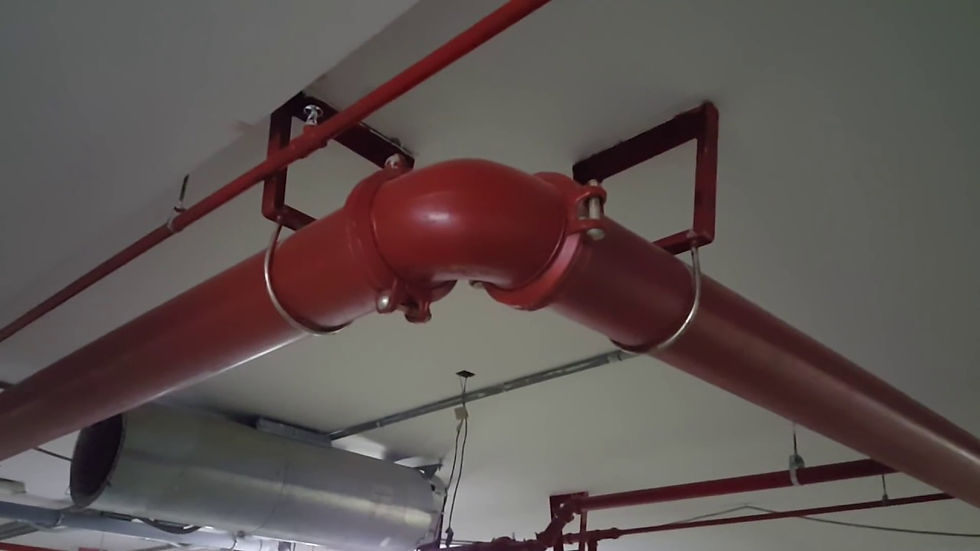
The Moody Chart
The Moody Chart finally provided a method of finding an accurate friction factor. This encouraged use of the Darcy-Weisbach equation, which quickly became the method of choice for hydraulic engineers.
The introduction of the personnel computer from the 1980s onwards reduced the time required to calculate the friction factor and pipe head loss. This has widened the use of the Darcy-Weisbach formula to the point that most other equations are no longer used.
Hazen-Williams Formula
Before the advent of personal computers, the Hazen-Williams formula was extremely popular with piping engineers because of its relatively simple calculation properties.
However, the Hazen-Williams results rely upon the friction factor's value, C hw, which is used in the formula. The C value can vary significantly, from around 80 up to 130 and higher, depending on the pipe material, pipe size and fluid velocity.
Also, the Hazen-Williams equation only gives good results when the fluid is water and can produce large inaccuracies when this is not the case.
The imperial form of the Hazen-Williams formula is: hf = 0.002083 x L x (100/C)^1.85 x (gpm^1.85 / d^4.8655) where: hf = head loss in feet of water L = length of pipe in feet C = friction coefficient GPM = gallons per minute (USA gallons, not imperial gallons) d = inside diameter of the pipe in inches
The empirical nature of the friction factor C hw means that the Hazen-Williams formula is not suitable for accurate heat loss prediction. The friction loss results are only valid for fluids with a kinematic viscosity of 1.13 centistokes. The velocity of flow is less than 10 feet per sec, and the pipe diameter has a size greater than 2 inches.
Notes: Water at 60° F (15.5° C) has a kinematic viscosity of 1.13 centistokes. Common Friction Factor Values of C hw used for design purposes are: Asbestos Cement 140 Brass tube 130 Cast-Iron tube 100 Concrete tube 110 Copper tube 130 Corrugated steel tube 60 Galvanized tubing 120 Glass tube 130 Lead piping 130 Plastic pipe 140 PVC pipe 150 General smooth pipes 140 Steel pipe 120 Steel riveted pipes 100 Tar coated cast iron tube 100 Tin tubing130 Wood Stave 110
These C hw values provide some allowance for changes to the roughness of the internal pipe surface due to the pitting of the pipe wall during long periods of use and other deposits' build-up.

Pipe Fittings Loss Calculations with K Factors
Pipe fittings, valves and bends usually have some associated K factor or local loss coefficient, which allows the calculation of the pressure loss by fitting for a particular fluid flowing at a specified velocity. Manufacturers of pipework fittings and valves often publish a fitting's associated 'K' factor.
Pipe Fitting Loss Formula
The following equation can calculate fluid head loss through a fitting: h = K x v² / 2g where
h = pressure loss in terms of fluid head, i.e. fluid head loss K = manufacturer's published 'K' factor for the fitting v = velocity of fluid g = acceleration due to gravity
The length of the pipe is relatively long. The effect of the fitting losses is usually considered minor losses and is often ignored during the pipe system's initial analysis.
If the piping design contains a partially open valve, engineers should always include the effect and heat loss through the valve since the valve head loss may be significant.
Pipe Fittings and K factors database
Our Pipe Flow Expert software has a database that contains the K factors for many different types of valves and fittings. It also has special wizard helpers that can calculate the K factor for special types of fittings such as:
gradual enlargements
gradual contractions
sudden enlargements
sudden contractions
rounded entrances
long pipe bends
Equivalent Length of Pipe for Pipe Fittings
Sometimes the pressure loss of a fitting is expressed as an 'Equivalent length' of pipe, whereby the engineer calculates a further length of pipe that will produce an extra friction loss in the pipe that is equivalent to the loss through the fitting. In this way, adding a notional extra length to each pipe can model the further pressure loss that would have occurred due to the fittings.
The 'K' factor of a fitting may be calculated from the 'Equivalent length' (in m or ft.) if the friction factor and the Internal diameter (in m or ft.) are known.
The 'Equivalent length' and 'Internal diameter' must be in the same units to calculate the 'K' factor.
K = (EL * ff) / i.d.
where:
EL= Equivalent length of pipe (in m or ft)
ff = Friction factor
i.d. = Internal Diameter of the pipe (in m or ft, same as for EL)
Friction Factor Calculations
For calculating the friction loss in a pipe, the Darcy-Weisbach equation uses a dimensionless value known as the friction factor (also known as the Darcy-Weisbach friction factor or the Moody friction factor), and it is four times larger than the Fanning friction factor.
Friction Factor Chart / Moody Chart
The friction factor or Moody chart is the plot of the relative roughness (e/D) of a pipe against Reynold's number. The blue lines plot the friction factor for flow in the chart's wholly turbulent region, while the straight black line plots the friction factor for flow in the wholly laminar region of the chart.

In 1944, LF Moody plotted the Colebrook equation's data, and the resulting chart became known as The Moody Chart or sometimes the Friction Factor Chart. This chart first enabled the user to obtain a reasonably accurate friction factor for turbulent flow conditions, based on the Reynolds number and the Relative Roughness of the pipe.
Friction Factor for Laminar Flow
The friction factor for laminar flow is calculated by dividing 64 by Reynold's number. Friction factor (for laminar flow) = 64 / Re
Critical Flow Condition
When flow occurs between the Laminar and Turbulent flow conditions (Re 2300 to Re 4000), the flow condition is critical and difficult to predict. Here the flow is neither wholly laminar nor wholly turbulent. It is a combination of the two flow conditions.
Friction Factor for Turbulent Flow
The friction factor for turbulent flow is calculated using the Colebrook-White equation:

Due to the Colebrook-White equation's implicit form, the calculation of the friction factor requires an iterative solution via numerical methods.
The friction factor is then used in the Darcy-Weisbach formula to calculate the pipe's fluid frictional loss.
Comments